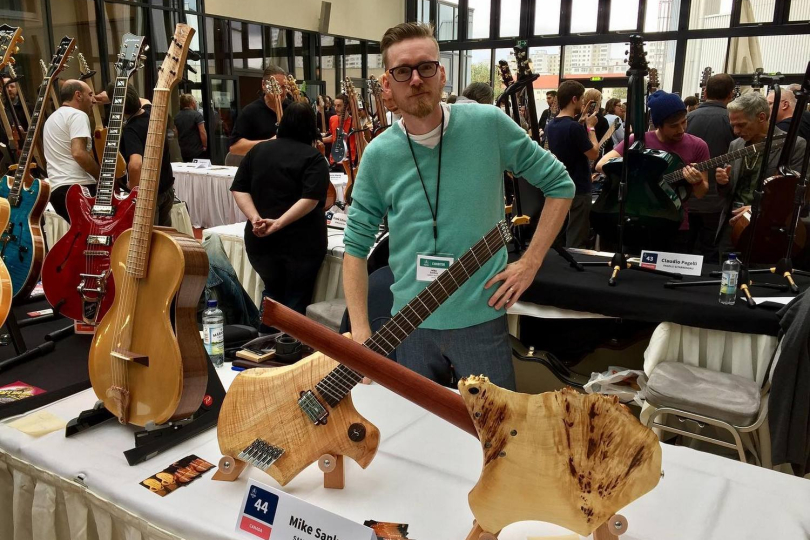
Dreamstruments #29: Sankey Guitars
In this series, we often hear of certain stereotypes like "he studied design or visual arts", "guitar player who modified his instruments for so long that he started making them", "my dad was a carpenter or (straight up) an amateur guitar maker" etc. Even though, it seems that these guitar makers are produced on an assembly line, their products are completely different every time. Today, we're looking at Mike Sankey, originally a Canadian guitarist, who started making his instruments while studying visual arts and, for inspiration, he studied the viola da gamba his dad built. But when working, he got completely away from any baroque influences.
In many ways, today's guitar makers have a freer hand than their predecessors. CNC, 3D printing and other technologies are much more readily available to them than they were just a few years ago. But the technology itself is useless without an idea and a clear vision. So many guitar makers are going back to the idea that handmade is best in the end anyway. The results may not be uniform, but that's often to the benefit of the cause – after all, no two pieces of wood grew exactly the same, so why should we try to make two of the same instrument?
Many makers work with this philosophy, often letting the wood dictate the final shape of the instrument. This is the case with Mike Sankey's Hi-8 guitar, for example, who says, "Given a knife an awl and some string I can make a guitar, and I could make those myself if I had to".
The first instrument was not impressive
"I made my first guitar when I was 19 and studying visual art in university. It was way too ambitious for a first guitar – a thinline acoustic archtop guitar with both electric and piezo pickups! It was made of garbage, literally: thin birch plywood from a door, some scraps of wood leftover from a flooring project. The pickups, knobs and even the tuners were all from the “misc” buckets of a couple of local guitar shops. High arch, flat back. Still got it, still works. I eventually presented it as a school project. It did not impress. I made a bunch of other musical sculpture types of things for school too. They were often not well received – my sculpture professor was hearing-impaired, old, and cranky," Mike confides in an interview with Breakthrough guitar.
Other guitars have been semi-hollows as well, and Mike has no scruples to admit that they didn't make him successful with the guitar community at first. In his hometown of Ottawa, he offered the instruments in music stores at almost dumped prices, and although they garnered positive feedback, no one took them off the rack. Mike even tried to move to a bigger city, but he also came off badly from Toronto. It wasn't until he started working as a guitar repairman back in Ottawa that he saw his first sales. By this time he had been making instruments for almost ten years!
The problem isn't inspiration, it's repetition
Mike admits he doesn't have much in common with traditional guitar makers who have a polished catalogue of instruments from which customers can choose. His approach is more about new paths, he's not keen on repeating what's already been built. Still, he has a distinctive handwriting and his guitars bear clear hallmarks. Often they are headless, with unconventional wood finishes, or proudly bear features that others would consider defects – these are something Mike emphasizes in his performance, as recycling and responsible use of available materials is also part of the process for him.
The problem for Mike, however, is not creating new shapes on paper, but assembling them. He admits that coming up with ideas is a chore for him, but he adds unequivocally that this task takes its place in his work rhythm and that he constantly has twenty to thirty unused designs in his workshop.
Fascinated with Japan
Mike Sankey's work has recently been influenced by Japanese culture. The names Tataki, Sakura, Mokugyo and Tachi clearly reveal their origins. What is interesting, however, is that this is not an empty nomenclature.
Mokugyo, the "wooden fish", has its origins in the ritual slit drums used by monks in ceremonies and perfectly demonstrates another typical feature of Mike's vision – innovation. In the case of this guitar, it is a combination of solid body and hollow body guitars within a one-piece poplar body. The carved slit in the bass side adds resonance and fundamentally changes the sound of the instrument.
Mike carved the guitar's slit with a special long chisel that he made himself (remember the quote from the beginning of the article – a knife and awl... I could make those myself if I had to...). But that's not to say that Sankey guitars don't have a 21st-century touch. Aside from the modern approach in construction, using carbon reinforcements in the necks to make the necks as thin as possible, they have another unique feature – 3D printed metal hardware. Mike uses hardware partly from reputable brands, but due to special requirements and modifications he modifies it with 3D printing or creates it himself.
Man cannot live by guitar alone
Being an independent luthier is no bed of roses. Once you've managed to get enough customers, you're struggling with time pressure, not always completely reliable suppliers and other minor and major problems – and you're usually on your own. Mike estimates that he has to make about one instrument a month to keep everything working as it should. But he doesn't hide the fact that in 2023, for example, nine guitars came out of his workshop. But he says he won't stress about it.
Mike's approach may be partly the result of a certain privilege, as he makes no secret of the fact that his wife provides for his family financially, but he is also the prototype of sound thinking. He doesn't chase success in product quality and lets his creative self breathe. He prefers a happy family. And it shows in his work. Each piece is an original, perfected down to the last detail.
If you have found an error or typo in the article, please let us know by e-mail info@insounder.org.