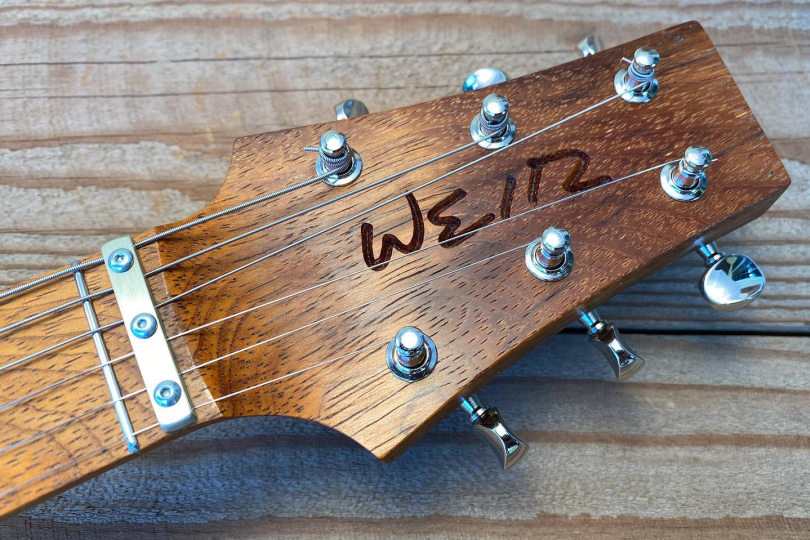
Dreamstruments #13: Dave Weir (Weir Guitars)
Most electric guitars today look more or less the same. A couple of basic shapes based on Gibson and Fender work, one or two neck cutaways, two or three pickups, two to four pots, a three- to five-position selector and a tremolo or adjustable bridge. Dave Weir, the author of the guitars in today's episode, goes in the opposite direction. No knobs, no cutaway acoustic shape, one neck pickup and a filed piece of iron serving as a bridge. Do you want something extra? Hard lines! "I probably turn away more orders than I take because they want something I don't want to or can't do," Dave admits. But the more you look at it, the more you see it the same way. The bottom line. Down to the core. No nonsense. Weir guitars.
Why try to cater to every guitarist's wishes when there's such a wide range of guitar makers? After all, it's impossible to please everyone. One man's trash is another man's treasure. Dave Weir of Escondido, California, has understood this to a T. He seems content to do his own thing, his own way – and the rest of the world leaves him cold. In fact, when asked for his photo to be used as the cover picture for the article, he replied laconically, "I didn’t come up with any pictures I want to share. The shop really is quite a mess."
Bare bones, rock solid
Of course, when it comes to his own formula for making instruments, it's not just any. Dave describes it as "bare bones and rock solid". The necks of his instruments, including the fretboard, are one piece. No "cut and glue", Dave fits the adjustable truss rod into the solid neck with fretboard through a single hole, specially drilled with a lathe. The truss rod itself then needs to be made to go in and work properly.
The pocket on the guitar’s body into which the neck is inserted before it is screwed together is slightly smaller than the neck itself. "Most people make the neck so it slips into place. We make the pocket slightly smaller than the neck. The neck is forced into place with a fair amount of pressure. There is the chance that the pressure will split the body open,” Dave admits. I think it’s a big part of the sound I get out of these things. But it’s a bit like a high-performance race car. On the verge of catastrophic failure. I’ve had a couple of breaks on installation. I’ve not heard of any breaking after they are out in the wild." That kind of neck and body connection is definitely rock solid then.
Necessity is the mother of invention
Inspiration sometimes comes from unexpected places. With Weir guitars, on the other hand, it was quite simple. Dave is left-handed and as a guitarist, he often had to adapt his playing to right-handed guitars. The pots bothered him, so he got into the habit of putting them on full and pushing them inside the guitar's body so he wouldn't graze against them. He decided to just not use them at all on his instruments.
As a left-handed player, he couldn't even use the cutaways on the guitar body for easier access to higher frets, so he didn't cling to that feature either. "I didn’t see anyone really doing a basic OO type solid body, so I went with it. My main focus on the body is that it be comfortable and have good balance. Things like Les Pauls and Jazzmasters and SGs look great, but they don’t balance well," Dave explains.
Minimal moving parts
When looking at Weir guitars, the more observant will notice that the jack isn't just any jack, it's integrated into the strap button, as is often the case with acoustic guitars. "I like the idea that parts have multiple functions, reducing the number of parts. The bridge was designed to really cut down the number of moving parts and parts in general. I feel like all those little screws and saddles in a typical bridge bleed off the string energy," Dave explains. "I’d like to think that by having a very solid take-off point, the string energy is either reflected back or transferred onto the body. A lot of people won’t notice little things like that, but I think it sounds better when all the parts are really tight and solid."
One pickup is enough
It wasn't so much an aesthetic decision as it was about following the aforementioned "bare bones" approach. "I’ve added a volume control a couple of times, but I always wish I hadn’t. I don’t like the extra parts or the extra work, or really even the end result. Two pickups really open up a can of worms. Of course, you need a switch, volume control to balance it out, and tone control to knock some of the high ends off the bridge pickup. That’s a lot of extra stuff. I think we actually turn away more orders than we take, because it’s off our path," Dave muses.
"It’s funny," he adds "how many people start out saying they love the minimalist aesthetic, and then ask for complications. Double neck, fan frets, nine strings, midi, etc. All that stuff is cool, but I’m really just trying to keep it simple. Other people have a business model that accommodates a lot of customization. It often gets pretty expensive. I like to just follow my own ideas. You can choose the wood and finish, and then a few body shapes. It’s a small menu."
Two dozen a year
Dave started making instruments about eleven years ago. His first attempt came from the simplest idea: "If I took a two-by-four and shoe-shined it with a strip of sandpaper it would eventually turn into a parabola, which is a good shape for the back of the neck." Dave was certainly not wrong, but he found out that the same result could certainly be achieved more quickly. A couple of years later he was making whole guitars and, as he admits, has been making about two pieces a month for some time.
"There are lots of easier ways to make money than making guitars. I see them more like art/engineering projects. I really enjoy the challenge of figuring out how to do things with the resources we have, and designing something a little different than what everyone else is doing. There is a small niche market of people that share my vision, and it’s fun to build for them," concludes Dave.
If you have found an error or typo in the article, please let us know by e-mail info@insounder.org.